EX
seamless backpack with insect-based chitosan used in a cascading system
EX is a backpack that cleans wastewater, saves material and is fully recyclable. This is made possible by the unique cascade usage of the bioplastic chitosan. The chitosan used for EX is obtained locally from the exuviae and exoskeletons of insects. In the EX concept, the chitosan is initially used to purify dyeing wastewater from the textile industry, as it has the ability to bind dyes. The coloured chitosan is then used to manufacture the backpack: pattern and functional elements are printed onto the cotton textile using chitosan. The chitosan bonds the textile layers seamlessly due to its stabilising and adhesive properties. At the end of its life cycle, the entire backpack can be shredded and processed into a new textile.
student: | Lena Muri |
project: | The Insect Project – Resilience Part I |
year: | 2023/24 |
EX is the prototype development of a material examination of chitosan in the textile industry.
Chitosan is a bioplastic that can be obtained from the exoskeletons of crustaceans and insects or from fungi. Due to its positive charge, the material has the property of binding the smallest color particles from textile dyeing waste water. It is therefore already being researched as a binding agent for dyeing wastewater. In current water treatment processes, however, all dye pools are mixed and only filtered afterwards. As a result, the dye and binder become a waste product or sewage sludge. The EX concept starts at an earlier stage in order to reuse both dye and binder. For this purpose, a chitosan filter is used directly after a dye bath. The filter removes dye residues from the water and pre-cleans the waste water. This subsequently reduces the formation of sewage sludge. The chitosan from the filter has now taken on the colour from the dye bath. In the next step, the coloured chitosan is dissolved with the help of acetic acid and applied to textiles as a printing compound.
In combination with textiles, chitosan shows stabilizing and adhesive properties. The cut and various functional elements have been printed on EX. Functional elements include stabilizing side and bottom areas, reinforcements on the zipper, back padding, and strap holders. The back padding is printed on the left side of the fabric. Chitosan then bulges as it dries, creating raised areas in the fabric that are used as back padding. The print also prevents the cotton fabric from fraying. Seams can be closed by dissolving chitosan. The non-fraying and adhesive properties result in seamless connections.
For prototype construction, a 3D printer was used to print the elements. In an industrial process, it is conceivable that the printing could be carried out using a screen printing process.
To achieve stability in a backpack, plastic materials or plastic coatings are usually used. In addition, materials are used for back padding, fastening straps and threads for seams. By printing the functional elements and gluing the seams together with the dyed chitosan, at least the materials mentioned above can be saved. It also makes it easier to separate or recycle the backpack at the end of its life cycle.
To recycle the backpack, the straps and zippers are detached from the textile and can be reused if necessary. The remaining fabric is shredded into fine fibers. The chitosan print is then dissolved by adding acetic acid. This reactivates the adhesive properties of chitosan and the chitosan binds the shredded fibers together. This creates a new textile or fleece, which is then used as a lining in a new backpack.
In summary, the bioplastic chitosan purifies textile wastewater, recycles dyes and, like the exoskeleton of crustaceans or insects, gives shape to a previously soft textile.
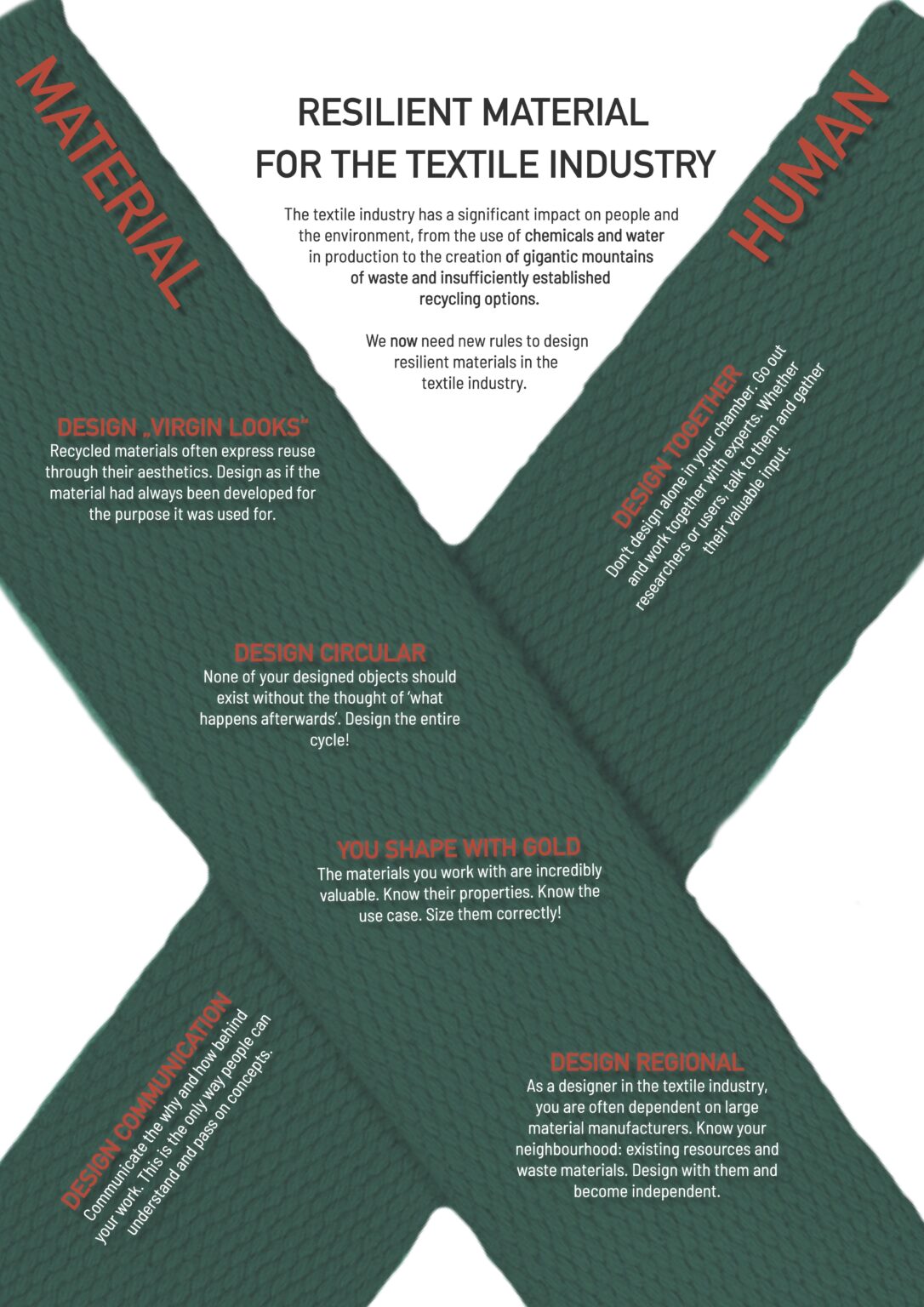